高新技术企业ISO9001
服务热线:135-3042-8982
塑料焊接工艺在汽车内饰产品上应用
塑料材料轻、可塑性强、经过皮纹处理后手感好,广泛应用于汽车领域。当今汽车产品上,在内饰仪表板、副仪表板、门护板、杂物箱盖、立柱护板等零件上,均采用不同材质的塑料进行加工。据统计,汽车用塑料品种目前已达几十种,平均每辆汽车塑料用量已占汽车自重的 5 % ~10 % ,随着汽车轻量化的发展要求和汽车塑料技术的扩大应用, 汽车塑料的单车用量今后还会进一步增加。 塑料零件目前基本通过卡接、螺钉连接、粘接 和焊接等方式进行连接。卡接、螺钉连接速度快,适用性强,但会产生应力集中,且不能有效形成密封连接,在某些环境下不适合采用。粘接能获密 封接头,但操作困难,需要精确地对接,而且速度很慢,不适于大批量生产。而焊接简单、快速、可 靠、准确,能形成强度接近于母材的接头,适合于大批量生产,在汽车工业快速发展的今天,获得了愈来愈广泛的重视。
常用焊接工艺
塑料分为热塑性和热固性两种,基于两种塑料的物理特性,焊接工艺只局限于热塑性塑料。 塑料焊接方法分为两大类:一是内部生热法, 通过机械运动使塑料内部摩擦生热进而融化,从而使塑料焊接在一起,如振动摩擦焊;另一类是外部加热法,通过外部加热设备使塑料融化而焊接在一起,如热气焊等。下面介绍三种应用较为广泛的焊接技术。
热板焊
热板焊是应用比较广泛且加工方法最为简单的塑料焊接工艺之一。焊接过程中,随型加热板放入两零件之间,并对零件进行加热至熔化温度, 然后取出加热板,对零件进行加压力,使熔化的焊筋贴合在一起,在可控压力下冷却和凝固而形成焊接,见图1。
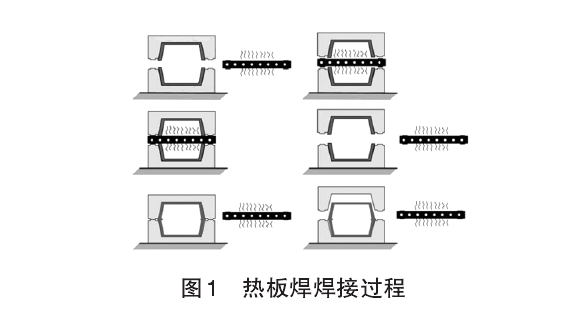
加热板由金属制成,通过内部的管状加热丝或释热元件加热,同时使用温度传感器对加热板表面的温度进行精确控制.加热板表面一般温度为180~230 ℃( 取决于材料类型 ) 。 焊接筋通常与基材相同。能加热熔化的塑料均可用热板进行焊接。热板焊也可用于不同基材的塑料焊接,这时零件的两部分分别采用不同的表面温度进行加热熔化.热板焊的焊接范围从直径几厘米到 1.5m的零件。热板焊可以形成良好密封连接,可以焊接表面不平整零件,但焊接连接结构相对复杂,加工速度慢。焊接时间从10~20s至 30 min 以上,视零件的大小及厚度而不定,有些大型厚壁零件的加热熔化时间甚至达1个半小时。
振动摩擦焊
振动摩擦焊是利用电磁传动装置使两塑料零件产生相对运动,通过摩擦在零件内部产生热量进而熔化基材后,让两零件焊接到一起的方法,见图2 。零件在压力作用下进行直线往复运动使零件内部产生热量,当温度升高到熔点后,材料熔化 且运动停止,零件在压力下凝固而形成焊接。振 动摩擦焊的主要工艺参数是:振动频率 100~500 Hz 、振幅 0.15~5 mm 、焊接时间 1~10 s 、焊接压力 1~ 4 MPa 。振动摩擦焊几乎能焊接各种成型工艺加工的零件。
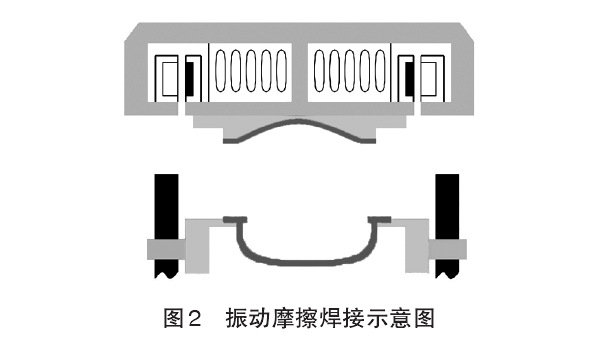
振动摩擦焊的优点是生产效率高、可以焊接 复杂连接零件。振动摩擦焊过程可控、不会出现 因过热而引起界面材料降解;缺点是只能焊接曲率小的零件。 振动摩擦焊在内饰产品上最有价值的用途之一是仪表板本体与风道的连接,通过振动摩擦焊接使两零件连接即形成用于空气流动的封闭空腔,又使仪表板本体得到加强,简化了仪表板本体骨架的结构,降低模具成本。
超声波焊接
超声波焊接是在压力作用下,使用高频机械振 动 ( 频率为 10~70 k Hz ,振幅为 10~100 μm) 使塑料零件内部产生热量熔化而形成焊接,见图 3 。超声波焊连接结构必须专门设计,以便将振动能量集中到熔化点。超声波焊接主要有两种连接结构:第 一种结构采用三角形凸台焊筋作为焊接接头 ( 高 0.2-0.8 mm) ,与之配合结构为平面,能量集中与三 角形凸台尖部,便于快速熔化材料;第二种结构是剪切接头,通常一个零件大于另一个零件,这种结 构无能量集中筋,发热主要是摩擦力实现的。超声波焊效率极高,焊接时间从 0.5~1.5 s ,可实现自动化,在内饰产品很多零件上都有应用。超声波焊接灵活,适应性强,通过使用不同类型的焊头,实现各种类型焊接需求,在内饰产品上主要应用超声波铆焊和超声波对接焊两种焊接形式,两种焊接型式均利用超声波在被连接表面的垂直方向上的振动来实现。
在汽车工业迅速发展的今天,内饰产品设计也正向多元化方向发展,产品的造型、重量、成本、 材料回收率等都影响着产品设计,而塑料焊接技术的应用使内饰产品在多方面综合因素的影响 下,最大化的体现造型设计思路,降低了内饰产品结构复杂程度、零件的重量、标准件数量、人工装配时间,提升了材料回收率,为大规模生产、模块化装配提供条件。可以深信,各种塑料焊接方法必将在汽车工业发挥越来越广泛的作用。